A Metal SIP plant can be designed to meet specific
production needs by purchasing various combinations of units. Each plant
can be customized to produce different profiles, panel widths, core
materials, end cuts, etc… The following describes each of the different
units. |
Roll Forming & Laminating Units |
Main Press
The Main Press is the heart of the Metal-SIP-Lock process. The Press
roll forms a male and female joint in the upper and lower coil skins
which is then laminated to a core insulating material through the
application of a two part polyurethane adhesive and a series of pinch
rollers to form a continuous length laminated panel.
The main press is operated from a main control console located in close
proximity to the Press to enable the line operator to closely monitor
and control the manufacturing process.
|
|

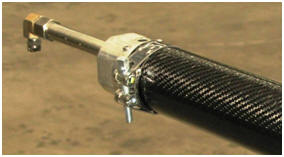
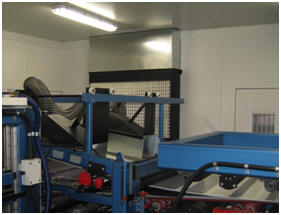 |
Spray Glue System
The Low Pressure Self Cleaning Spray Glue
System has been specifically developed for the continuous application of
2 Pre-mixed Part Polyurethane Adhesive for the lamination of Sandwich
Panel Production. The System is suitable for the lamination of most Core
Material types including EPS (Expanded Polystyrene), Mineral Wool (Slabs
or Lamellas). The System may be connected to Gravity Fed Standard 200
Litre Adhesive Drums or 1,000 Litre Industrial Bulk Containers, although
it is important to temperature control the adhesive. System is also, in
most cases, capable of use with a variety of 2 Part Polyurethane Brands
in different mix ratios. The system is capable of retro fitting and
integration with most Sandwich Panel Laminating Lines, regardless of
manufacturer. |
|
Deep Profile Roof &
Decoiling Unit
The Deep Profile Unit expands the capabilities of
a Pglant for
the production of rib roof panels. Located at the start of the line,
this unit roll forms continuous length steel coil into a rib roof
profile. The unit can be manufactured with the option to produce
profiles with 3, 4, or 5 ribs. The roll formed steel sheet is then feed
into the Main Press where it is laminated as the top skin with the core
insulating material and the underside steel skin.
|
Insulation Loading Units |
EPS Loader
The EPS Loader is used to load sheets of Expanded Polystyrene (EPS) into
the main press. A stack of EPS sheets are loaded by forklift into the
magazine of the unit. The sheets are automatically dropped onto the
cross feed table and pneumatically aligned to a datum point, ready for
lamination in the main press. An alarm is activated when the stack of
EPS is running low in the magazine. |
|
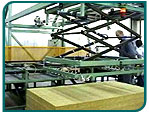 |
Mineral Wool Loader
The Mineral Wool Loader uses a lifting head and specially designed
needles to pick up the wool sheet and places the sheet onto the pusher
table which feeds the sheet into the main press. |
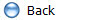
Cutting Units |
5 Position Steel Cut-Off
Unit
After the panel has been laminated through the main press the panel runs
through the Steel Cut-Off Unit. Notches are made into the male and
female roll formed edges of the steel skin and the panel is
simultaneously cut. The cuts are made 'on the fly' without slowing the
line speed.
|
|
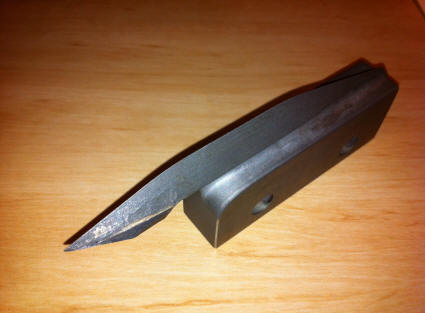 |
Silent Cutter
CO-345 Silent Cutter provides a perfect rounded finish to the
metal-sheet, while avoiding injuries. |
|
Coldwire Unit
After the steel panel has been cut the fully automated Coldwire Unit
uses an abrasive wire band mounted between two fast spinning wheels in a
floating harp to cut through a variety of core insulating and fire
resistant materials including mineral wool, polyurethane, P.I.R., XPS,
EPS or phenoelic panels. A vacuum unit cleans and collects any shavings
or debris left from the cutting blade. |
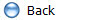
Packaging Units |
Panel Unloader
The unit operates by receiving newly laminated and cut panels from the
run-out conveyors. The finished panels are unloaded and stacked with
specially designed arms. In order to maximize panel stack heights of
Deep Profile Roof Panels The Turnover Unloader Unit alternates the
stacking of each panel. |
|
Stretch Wrapper
The stretch wrapper is designed to wrap packs of panels. The unit
consists of in-feed conveyors, a tunnel wrapping unit and out-feed
conveyors. Special pallets are placed on the feed conveyor, which are
loaded by the Unloader Unit. Each pallet travels along the conveyor into
the tunnel where a ring rotates around the pack with shrink wrap as it
travels through. |
|